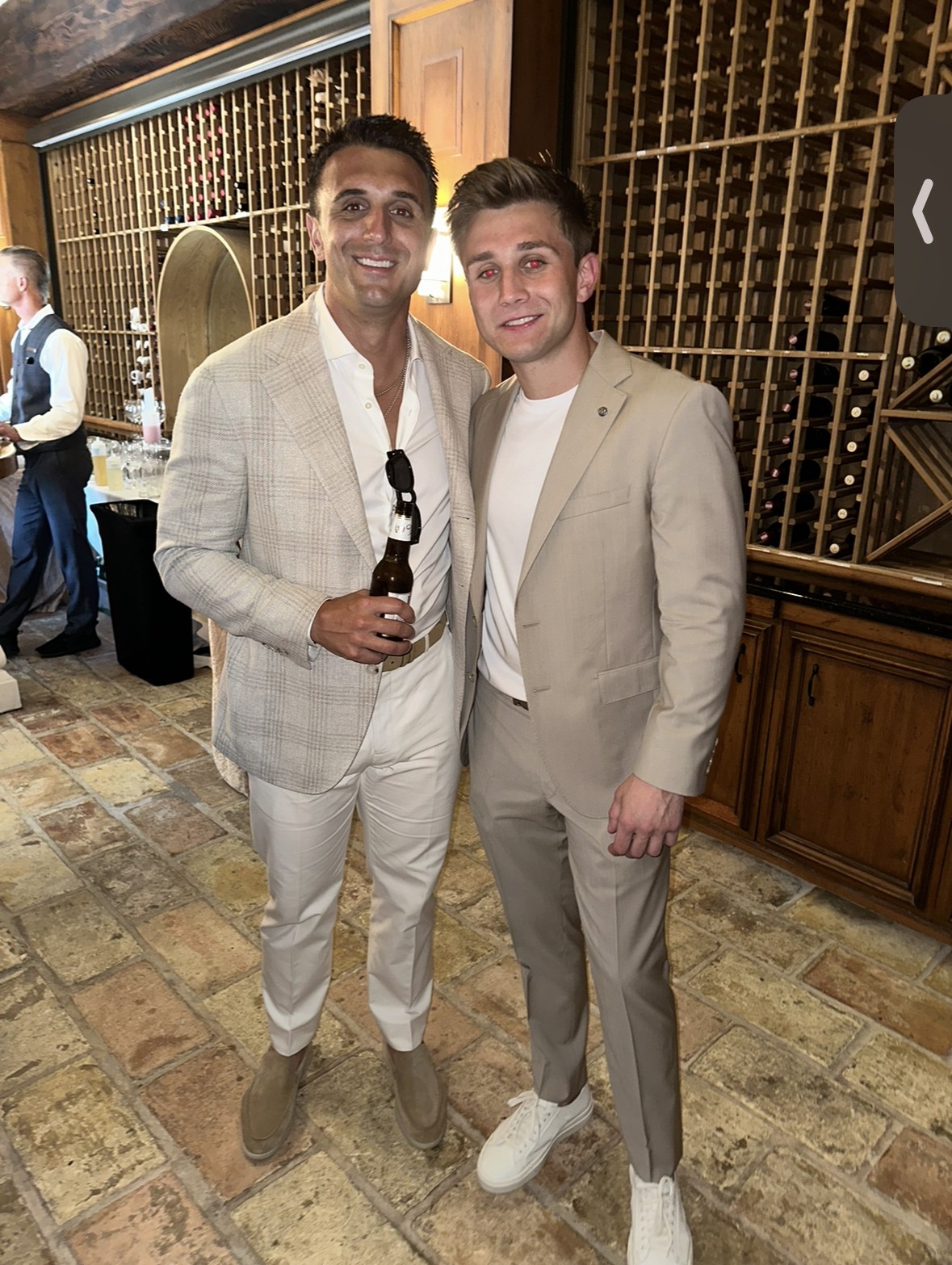
Warehouses are the backbone of many industries, from retail to manufacturing, and optimizing their operations is essential for maximizing profits. As businesses scale and customer demands grow, streamlining warehouse processes becomes even more critical. Let’s explore how you can maximize both efficiency and profitability in your warehouse operations.
Embrace Automation and Technology
One of the most effective ways to boost warehouse efficiency is by adopting automation and technology. Automated systems, such as conveyor belts, automated guided vehicles (AGVs), and robotic pickers, can significantly reduce manual labor and the chances of human error. These tools ensure that products are moved and sorted quickly and efficiently, reducing bottlenecks and delays.
Moreover, implementing warehouse management systems (WMS) provides real-time data, which helps track inventory, monitor employee productivity and forecast demand. With a WMS in place, businesses can make more informed decisions, cut down on waste, and enhance order fulfillment processes. The initial investment may seem high, but the long-term returns in efficiency and cost savings are substantial.
Optimize Warehouse Layout
An efficient warehouse layout plays a significant role in streamlining operations. Proper placement of inventory and equipment can reduce unnecessary movement, saving both time and effort. Start by analyzing product demand. Frequently picked items should be located near packing and shipping areas to minimize travel time. Slow-moving products can be stored in less accessible areas.
The concept of slotting optimization can also be applied. Slotting refers to the organization of products within the warehouse based on factors such as size, weight, and picking frequency. By grouping items logically, workers can quickly locate and retrieve products, reducing the time spent searching through rows of shelves.
In addition, labeling and signage should be clear and consistent. Having well-marked zones for different product categories or sizes makes navigation more accessible, especially for new employees or temporary workers.
Improve Inventory Management
Efficient inventory management is crucial to avoiding overstocking, stockouts, and unnecessary carrying costs. Implementing barcode scanning or RFID (Radio-Frequency Identification) technology can achieve real-time inventory tracking. These tools allow accurate stock levels to be recorded and updated instantly, ensuring that your inventory records are always up to date.
Using techniques like just-in-time (JIT) inventory systems can reduce the amount of stock held on-site, lowering storage costs while ensuring that products are available when needed. Businesses should also conduct regular audits to verify that their inventory levels match the data in their management systems. Discrepancies can be costly, leading to delays, wasted resources, or even lost sales.
Train and Empower Employees
A well-trained workforce is essential for maintaining warehouse efficiency. Employees should be knowledgeable not only about their specific roles but also about the overall warehouse operations. This holistic understanding allows them to identify potential inefficiencies and suggest improvements. Continuous training on the latest technologies and safety protocols ensures that the team is well-prepared to handle evolving demands.
Empowering employees to contribute ideas for process improvements can foster a sense of ownership and motivation. Regular feedback sessions or suggestion boxes can help gather valuable insights from those working on the warehouse floor daily. After all, your workers are often the first to notice inefficiencies that management might overlook.
Focus on Safety and Ergonomics
Safety is paramount in any warehouse environment. Accidents harm employees and can result in costly delays and product damage. To maximize efficiency, robust safety protocols must be implemented and enforced. Regular safety training and inspections should be conducted to ensure compliance.
In addition to safety, ergonomics plays a significant role in warehouse productivity. Poor ergonomic conditions can lead to worker fatigue or injury, decreasing efficiency. By investing in ergonomic equipment, such as adjustable workstations and easy-to-use lifting tools, you can reduce the strain on your workforce and improve overall performance.
Streamline Shipping and Receiving Processes
The efficiency of your shipping and receiving processes can have a direct impact on warehouse operations. Delays in these areas can cause congestion and slow down the entire system. To avoid this, create standardized procedures for receiving goods, such as setting specific time slots for deliveries or establishing guidelines for checking and unloading shipments.
Implementing cross-docking techniques, where incoming goods are transferred directly to outgoing shipments without being stored, can also reduce handling times and lower storage costs. This method is especially effective for high-turnover items.
Another helpful strategy is using batch picking for orders, where multiple orders are picked simultaneously, reducing the need for repeated trips to the same areas of the warehouse. This technique improves the speed of order fulfillment while lowering labor costs.
Leverage Data Analytics
Data is a powerful tool for identifying inefficiencies and opportunities for improvement in warehouse operations. By analyzing data on order fulfillment times, picking errors, and stock levels, businesses can make informed decisions to optimize their processes. Predictive analytics can also help forecast demand, allowing warehouses to adjust their staffing and inventory levels accordingly.
Moreover, key performance indicators (KPIs) such as order accuracy, inventory turnover, and shipping times can provide a clear picture of how well your warehouse is performing. Regularly reviewing these metrics helps identify areas that need attention and allows for continuous improvement.
Sustainability and Cost Reduction
Incorporating sustainable practices into warehouse operations can lead to both environmental benefits and cost savings. Energy-efficient lighting, recycling programs, and reducing packaging materials are just a few ways to lower operational costs. Additionally, optimizing transportation routes and reducing the frequency of shipments can decrease fuel consumption and lower emissions.
Sustainability isn’t just about reducing costs—it’s also a key component of corporate responsibility. Many consumers prefer to engage with businesses that prioritize eco-friendly practices, which can enhance your brand image and customer loyalty.
A Well-Oiled Machine for Profitability
Maximizing efficiency in your warehouse is a more than one-size-fits-all approach. It requires a combination of technology, intelligent inventory management, well-designed layouts, and empowered employees. By continuously analyzing and improving your processes, you can transform your warehouse into a well-oiled machine, driving profitability and customer satisfaction.